Johannes Helmich, chief technology officer at TI Fluid Systems, lifts the lid on how technical innovation in thermal management is evolving the automotive industry’s transition to electrification.
It is an exciting time to be involved in automotive engineering. As the industry accelerates towards electromobility, engineers across the automotive supply chain are being challenged to innovate and adapt like never before.
In my role as chief technology officer at TI Fluid Systems, I see these challenges – and the opportunities they present – firsthand. With overall responsibility for the company’s technology roadmap, I am charged with keeping abreast of what the market requires from a technological point of view and ensuring that our product portfolio and strategy develop in line with market needs.
I am lucky that I can lean on the engineering expertise and knowledge gained from TI Fluid System’s 100-year history of producing fluid handling products. But to really meet the needs of the modern OEM, one must also think outside of the box, complementing this technical know-how with new techniques, new processes and constant innovation.
This is the challenge that presents automotive manufacturers and component suppliers the world over – ensuring that product development and process capabilities are fit for purpose in the era of electrification. But before I go any further, it’s important to understand the drivers of change and how these relate to thermal management.
Put simply, the significantly increased requirement for thermal in electric vehicles boils down to efficiency. And that all starts with the motorist. One of the chief concerns of electric vehicle buyers is of course driving range, and this presents a major challenge to OEMs. They must develop new technologies that deliver increased efficiency and range, and they must do this at a quickening pace and on an increasing scale.
However, there are a number of technical barriers to achieving this. For instance, electric vehicle batteries perform at their best within a specific, and narrow, temperature range. If the temperature gets too low, then the battery performance and efficiency are negatively impacted. Too high and the performance is also negatively affected, and above a certain temperature, permanent damage will be caused. When an electric vehicle is in operation, the battery’s temperature can be affected by the external temperature, charging, overuse, and myriad other factors, which makes temperature regulation difficult.
This is where thermal management comes in. To enable a battery to stay within its narrow operating parameters, we must control its temperature effectively. The same principles apply to the electric drive system. If you want to produce a compact and efficient electric drive architecture, you can’t do it without effective thermal management.
And that, in basic terms, is why thermal management has become even more important in the hybrid and electric vehicle space. Finding new ways of controlling the thermal flow of increasingly complex vehicle architectures, to enable them to run as efficiently as possible, is the name of the game.
Thermal management solutions
A key focus for TI Fluid Systems today is developing efficient and compact modular thermal management solutions. As I mentioned before, this necessitates a blend of experience and innovation. On the ‘experience’ side of the equation, we are taking our vehicle system competencies and know-how from both our tank and fluid carrying divisions and applying it to the development of highly effective and compact thermal systems.
By doing this we always revert to our core technologies. For example, we use our blow molding process, typically used to create fuel tanks, to provide coolant manifolds, as well as integrating functions for flow control – valves, pumps etc. – into these modules.
We are also looking at similar innovations in our refrigerant product line. Working with refrigerants comes with its own set of unique challenges, as you need to understand the thermal and chemical behaviors of different refrigerants under different pressures and temperatures – knowledge that TI Fluid Systems has in abundance. Again, the same principles of efficiency and compactness apply to refrigerant systems.
On the innovation front, an exciting advancement is the use of simulation technology to expedite product development and validation cycles. At our newly opened e-Mobility Innovation Center (eMIC), in Ratstatt, Germany, we can upload an OEM’s vehicle data and then display, analyze and redesign 3D models of thermal systems, modules and components within a full electric vehicle architecture.
This is all done using a high-resolution, 9-megapixel LED panel that measures 9 meters by 2.5 meters, which creates a simulated environment that really is a game-changer. It means that we don’t need to build the hardware in the early phases of the development cycle, so it’s incredibly time and cost effective.
Once we have simulated a compact, highly efficient thermal module within a given OEM’s architecture, we can then move on to designing the product, 3D printing it, assembling, testing and integrating it into the car, all under one roof at the eMIC.
This kind of end-to-end customer-focused solution is what the market is asking for; there’s a real appetite among the OEMs to work collaboratively on product development for their electrified vehicles because there’s no scope for wasting time. Our Ratstatt center is the first of five to open by 2023, so I expect TI Fluid Systems to be well positioned to capitalize on this emerging need for enhanced collaboration.
I think the key point I’d really like to drive home is that, in order to support the industry’s transition to full electrification, there can be no half measures. Component manufacturers and their engineering teams must be totally committed to embracing the changes ahead.
You need to accept the change, be prepared to invest in a new set of technologies, skills, software and mechatronics. You also need to invest in a different set of software architectures and tools, to empower your engineers to provide new products but also to deliver new and flexible manufacturing processes within a short time. You must be agile and constantly able to provide new innovations as the market continues to evolve.
Working together, the automotive sector can and will navigate the transition, and I’m proud to say that engineers will be at the very heart of it.
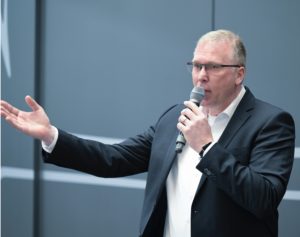