In an energy-conscious world, electric vehicles (EVs) have become the gold standard for road transport. The EV powertrain can achieve upward of 80 percent efficiency, easily trumping the compression-ignition internal combustion engine’s (ICE’s) thermal efficiency of about 50 percent. What is more, EVs and hybrids can also recover some of the kinetic energy from deceleration and braking that would otherwise have been lost to heat and friction. While Kinetic Energy Recovery Systems (KERS) are not new, the electric vehicle offers engineers new opportunities to simply and efficiently recuperate and store energy that would otherwise have been lost in an ICE vehicle.
The mechanical KERS designed for use with ICE vehicles at the turn of the century typically relied on a complex recovery and storage system, often requiring a constantly variable transmission to drive a high-speed flywheel housed in an enclosure at an almost perfect vacuum to store the energy. In contrast, the KERS designed for the electric powertrain requires no additional hardware – the existing traction motor that powers the vehicle acts as a generator when braking or coasting, with the energy thus harvested stored in the lithium-ion battery (LiB). This is referred to as regenerative braking, or simply “regen.”
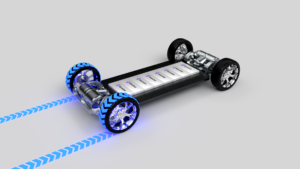
Powertrain potential
In an EV, the electric machine behaves both as a motor and generator at the same time. So, while acting as a motor to deliver power, it also generates a Counter Electromotive Force (CEMF) as a generator. But, because the CEMF is lower than the battery voltage the motor acts as a load and absorbs the current to do work.
However, as soon as the motor receives external mechanical power – from the drivetrain in the case of an EV – it inverts the current direction to charge the battery. Acting as a generator the electric machine also develops a counter torque that works as a brake during regenerative braking. These systems are so effective at recovering energy that Volkswagen claims that 20 percent of the energy used to power the I.D.R with its 45 kWh battery to a new record at the 2018 Pikes Peak hill climb came from regen.
The consensus view of the industry is that regen can recover as much as 60 to 70 percent of the kinetic energy ‘lost’ during deceleration or braking. This “round-trip efficiency” considers all losses incurred during the recovery of the kinetic energy, converting it to electricity, storing it in the battery, extracting it from the battery, and then finally converting it to tractive energy again.
Even though the energy harvested in this manner is significant, there are definite limitations on how much energy can be recuperated, with the LiB playing a pivotal role in determining this.
Batteries are key
The efficiency and amount of regen energy recuperation are largely determined by the Li-ion battery’s ability to accept the high rates of charge delivered during peak regeneration. This in turn is influenced by the capacity of the battery and its chemical composition and architecture. Small batteries with less capacity, such as often found in high-performance hybrid sports cars, have – due to the high peak regen – a limitation to the amount of charge they can accept.
Thus, a Ferrari SF90 Stradale with a 350-volt, 7.9 kWh battery could accept a maximum of 7.9 kWh (about 28 MJ) regen energy at 1C. With about 2 kWh of kinetic energy – the equivalent of 0.2C – being harvested by bringing the SF90 to a stop from 340 km/h, total energy recovery would seem well within the battery’s performance parameters.
This changes dramatically if the time to recuperate the energy is reduced. So, if the SF90, in the example above, is brought to a stop in 30 seconds (which is a relatively gentle stop) the C-rate jumps to 24C – far above the typical LiB’s capability. At this rate, the battery management system would have to limit the regen current.
Furthermore, in the typical LiB, the charging current is also not linear, being heavily dependent on the state of charge (SoC) of the battery. A battery at 80 percent SoC would accept a considerably lower current than if it was at 50 percent SoC. While small and mid-range BEVs face similar challenges to PHEVs, for luxury EVs fitted with larger LiBs with extra capacity to absorb the regen energy, this is less of an issue. On the other hand, larger batteries add unwanted cost and weight to the EV, while extending the time it takes to charge the battery pack. However, the fact that “wasted” energy can be recuperated and stored in the battery through regen holds the potential to reduce the capacity of the battery – with energy being added from regenerative braking to make up for the smaller pack.
The challenge to realizing regen’s full potential to recuperate this energy lies in the battery’s cells’ extreme fast charging capability.
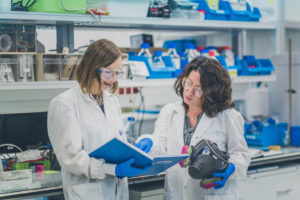
Unlocking regen potential
There are two major reasons for decreasing/limiting power during the charging: cell chemistry and pack cooling. In the case of regen, the cooling is less important, due to much shorter charging times. The most important parameter is the chemistry of the cell. When large currents are applied, the lithium plating rate can be much faster than the transport rate so that a huge concentration gradient forms at the growth front of the lithium. In extreme cases, Lithium ions would be depleted at the anode surface and even drop to zero.
This is exacerbated in the high state of charge regions where Lithium deposits tend to propagate into the decreasing regions that are available allowing for the formation of dendrites. So, for a typical lithium ion cell with graphite-based anode, applying a high charging current at a high state of charge is unacceptable, and could result in safety issues.
However, silicon dominant anodes, with at least 30 percent silicon by weight, inherently have a lower probability of dendrite nucleation and growth due to faster kinetics of the alloying reaction compared to graphite-based anodes.
The solution to the challenges current Li-ion batteries pose to regen’s potential to effectively utilize smaller, lighter, and cheaper battery packs such as StoreDot’s Extreme Fast Charging (XFC) EV battery. The battery cell technology developed by StoreDot, which uses optimized cell design and silicon dominant anode structure, is capable of extreme fast charging in a wide range of state of charge. Unlike most LiBs, the XFC cell does not degrade and there is no impact on its cycle-life typically associated with high charging rates. Both characteristics are ideal for optimizing the energy recuperation that allows manufacturers to reduce the size and cost of the battery pack while extending battery life.
Smaller battery packs
With manufacturers facing significant hurdles in wider EV adoption, including reducing the cost and time to charge for an acceptable range, extreme fast charging battery technology allows OEMs to re-evaluate their strategies in meeting these challenges. Smaller packs with extreme fast charging technology offer consumers faster charging, improved energy efficiency, increased utilization of regenerative braking, reduced carbon footprint, and lower costs. As a result, OEMs will be able to optimize a vehicle’s weight and cost, rather than pushing for ever greater range and battery size, making EVs more affordable and lighter, to serve a broader market and further speed up the adoption and transition to EVs.