Dominik Pawlik, product line manager at Interplex, looks at the various considerations that electric vehicle (EV) manufacturers need to be aware of in relation to powertrain interconnect implementation. It will outline the main engineering issues that are being faced, and then explain what can be done to overcome them.
Global EV uptake is increasing dramatically. Projections from Bloomberg NEF are now suggesting that their annual sales will reach 20.6 million by 2025 – which is more than triple what it was in 2021, and nearly 10 times what it was back in 2019.
In order to secure greater commercial traction and gain a competitive edge over their rivals, vehicle manufacturers are looking to boost the powertrain efficiencies of their models. This will mean that longer distances may be traveled between charges and charging times can be made shorter (both of which will lead to greater convenience for EV drivers). To achieve such heightened efficiencies, EV manufacturers are now designing in wide bandgap power switch devices (capable of operating at higher speeds) and raising the powertrain voltage from 400V to 800V (to minimize the associated power losses). Having better constructed interconnect components interfacing between a vehicle’s battery pack, inverter and traction motor will also make a significant contribution to such efficiency goals.
Another dynamic that is having major bearing on EV design, is the reductions being witnessed in system size and weight. The next generation higher power density EVs will feature smaller and more lightweight inverters and on-board chargers. This will help to make them more cost competitive and further extend the range that they are capable of supporting.
Automotive OEMs are promoting bus bars in EVs to replace traditional wiring, and by having more advanced busbar implementations, considerable electrical performance enhancements will be realized. At the same time, it will mean that the assembly processes involved can be made more straightforward, with production throughput thus being accentuated. The next few sections will look at the different areas optimization of busbar construction is possible.
While the dimensions of cabling alter (due to bending), busbars have fixed dimensions. The upshot of this is that the assembly process is much easier to automate. Bus bars will support shortened assembly time and internal material handling costs, both of which will be beneficial to automotive OEMs. In addition, bus bars are easy for modeling design, signal suppression and noise elimination.
Materials selection
There are different factors that will determine whether copper or aluminum conductors are employed in busbar construction. In situations where there are high temperatures, the thermal properties of copper will be advantageous – with greater ability to dissipate heat and a lower coefficient of thermal expansion (CTE). Copper conductors can also be substantially smaller, due to better conductivity – meaning they are better aligned with space constrained application environments. If keeping the overall weight of the system down is more of a priority, then aluminum conductors are likely to be the preferred option. Aluminum has a 70% lower density than copper and conductors using it will generally be around 50% lighter than their copper equivalents. They are also less expensive, making them appealing from a budgetary perspective. The attributes just described mean that copper is usually specified for automotive DC/DC converter busbars, while aluminum is used for busbars providing interconnection in battery cells.
There are a variety of different fill materials that can be used to isolate the busbars. These include polyphenylene sulfide (PPS), polyethylene terephthalate (PET), polybutylene terephthalate (PBT) and polyphthalamide (PPA). Which will prove to be most appropriate depends on the specific application criteria and the operating conditions. For example, in scenarios where there are high voltages to contend with, then the superior dielectric breakdown characteristics of PPA will probably be required. If extreme high currents must be handled, then PPS has superior insulation properties. Both the high-volume resistivity and insulation resistance are retained after exposure to high-humidity environments, and can be conveniently doped to achieve elevated conductivity. It is recommended that, thanks to its electrical conductivity, PPS (either p- or n-doped) is utilized as an antistatic coating to protect integrated circuits from static charges, humidity and corrosion at a system level around the busbar.
Cost will, once again, have an influence on which of these materials is chosen. It is important to recognize though that going for cheaper materials can impact on longevity. Even if a material comes with a higher price tag, the benefits that it brings in terms of protracted operating life can often easily justify this – resulting in a lower total cost of ownership (TCO).
Incompatibilities with regards to each of the constituent materials’ respective CTE figures will be problematic – as this causes contraction/expansion stresses to be placed on the busbar assembly when fluctuations in temperature occur. By choosing materials that have better matched CTE values, these thermal stresses can be lessened and the lifespan of the assembly will consequently be extended.

Mechanical aspects of busbar construction
In addition to temperature cycling, exposure to the ongoing vibrations found in automotive environments must be considered. To deal with both of these issues, adequate stress relief mechanisms need to be incorporated into the busbar assembly.
In some circumstances, flexible busbars will be the best option. These rely on thin high-conductivity copper foils, which are bonded together (via molecular diffusion welding) at the mounting areas. These can slide against one another – allowing an effective interconnect to be provided, even when the busbar is subject to vibrational or torsion forces.
It should also be mentioned that heat cycles can bring about the build-up of oxidation layers on copper and aluminum conductors. Such oxidation layers will add to the busbar’s resistance (and curb its performance). They can also shorten the working lifespan of the busbar. There are techniques that can be applied to prevent oxidation from occurring or at least mitigate its effects. Various noble materials, like Sn, Ni or Ag, can be applied on the surface of the copper to combat the oxidation effect. As the base of any bus bars will be manufactured using copper or aluminum, price fluctuations may significantly impact end product costs.
Also worth noting is that aacceptable tolerances must be built into the busbar structure, so that assembly issues do not arise.
Insulation challenges
It is critical that there is a good balance between the need for coatings and materials to have high dielectric strength and an elevated comparative tracking index (CTI) with resilience to extreme temperatures. Sometimes busbar internal temperatures can exceed environmental temperatures and this can present problems for the dielectrics in direct contact with them. Polyester coatings have high degrees of hardness and are very useful when chemical and physical resistance needs to be attained.
To maintain safety, the creepage and clearance that the busbar exhibits is also paramount – especially as busbar assemblies are getting more compact and the voltages they are dealing with are increasing. For this reason the materials used in busbars and their structural design need to be able to take this into account. Creepage/clearance distances can be increased by adding extra layers of the insulation foil to the assembly. Multiple discrete conductors, in both planar and stacked configurations, can be integrated into a single assembly. Creepage/clearance between conductive surfaces may be extended further by valleys and walls. Shallow or deep drawn contact surfaces can also be incorporated to accommodate the planar mounting surfaces of an IGBT or capacitor mounted directly to the bus bar.
With busbar implementations needing to take up less space, there are also technical challenges in relation to their attachment. The space limitations mean that the bolting, welding, or clamping of connections to busbars may not be possible. The use of soldering can be problematic for several reasons. Firstly, it adds another relatively time-consuming stage to the OEM’s manufacturing workflow (with what might otherwise be a fully automated process being interrupted by manual intervention). Secondly, it means that components within the sub-system will be exposed to heat that could mean that they are at risk of being damaged (thereby lowering the OEM’s production yield). Solder can have an effect on the CTE compatibility of the busbar assembly too. By having a solderless method for connecting busbars, all of these problems can be avoided.
To permit further space savings, in a growing number of cases busbar assemblies are starting to integrate additional system level functionality – so as to support other facets of the vehicle’s operation. Among the items now being featured are filtering components (to combat the presence of electromagnetic interference) and current sensor concentrators (to improve the accuracy of powertrain monitoring).
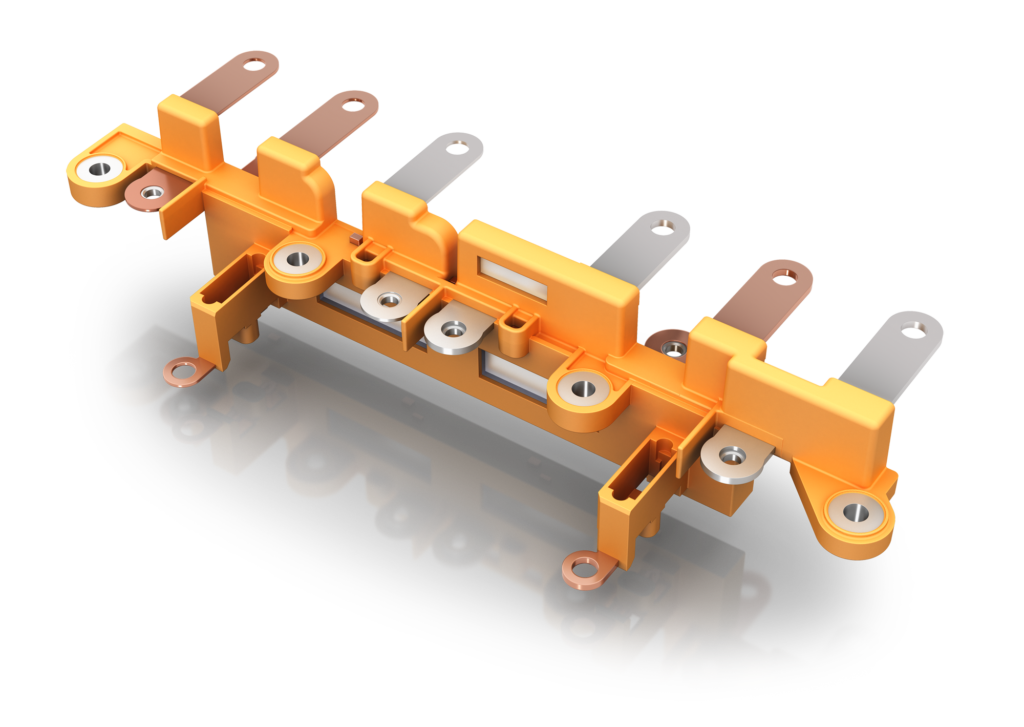
The complex molded busbars developed by Interplex offer the customer an optimized design balancing the need for cost, assembly process, weight, space and performance.
Conclusion
The interconnect expectations of the EV market are rising, as new models that push the performance envelope are introduced. Rather than having discrete interconnected subsystems, there is a migration underway which is moving the industry towards completely integrated systems. As well as helping to augment performance, this approach will enable cost savings to be witnessed, as it allows the number of parts to be rationalized. Furthermore, it means that the need for size and weight reductions can be addressed. Because of this, busbar integration into EV powertrains needs to be considered at a much earlier stage. It can no longer simply be treated as an afterthought, but must be acknowledged as an integral part of the design process.
The advanced multi-layer molded busbar products that Interplex offers are deployed in EV models from many of the leading manufacturers. They deliver the reliability, compactness, performance and TCO capabilities that are set to enable future EV powertrain objectives to be met. If you have any design questions or require assistance optimizing your design using busbars for your application, Interplex experts are available to help.
About the Author: Dominik Pawlik is a Product Line Manager at Interplex. He has over 20 years industry experience and a degree in mechanical engineering. Interplex is a world leader in designing and manufacturing interconnect and mechanical products and a go-to-source to solve complex design challenges for the e-Mobility market.