A UK-based company has unveiled its what it believes to be the world’s most sustainable motor for electric vehicles. Its new motors are completely free of rare earth magnets, yet are said to be able to offer all of the performance and efficiency benefits and more of a conventional permanent magnet motor, without their considerable environmental drawbacks.
Unlike today’s standard EV motors, its HDSRM and SSRD motors do not feature rare earth magnets so do not require the harmful mining of materials such as neodymium and dysprosium.
According to independent research, every tonne of rare earth material mined produces up to 1.4 tonnes of radioactive waste, 200m3 of acid-containing sewage water, 60,000m3 waste gas containing hydrochloric acid and 27.6 tonnes of CO2. Based on a global car production of 97 million vehicles, AEM’s technology could save the production of 133 million tonnes CO2 per year as well as 300,000 tonnes of radioactive waste.
Rare earths also appear at the top of most nation’s lists of critical materials, those where there is long term concern for security of supply. As a result of this uncertainty, the price of neodymium, which is commonly used in permanent magnet electric motors, has increased by more than 240% between March 2020 and March 2021, meaning that they are financially unsustainable as well as environmentally problematic.
As well as rare earth metals, traditional permanent magnet motors also use copper windings. At end of life, the copper must be removed from the motor before recycling, making the process difficult and expensive. AEM claims its technologies can be produced using only steel and aluminium, meaning that it can be recycled quickly, cost-effectively and completely.

HDSRM is a next-generation Switched Reluctance Motor (SRM) that, uniquely for this type of motor, operates with the standard power electronics used by most EV drivetrains. Its design and patented technologies claim that, unlike previous SRMs, HDSRM can operate quietly and with minimal torque ripple.
“From the earliest concept stage HDSRM was shown to match the performance of a leading permanent magnet motor of the same size while offering improved efficiency. It also delivers very robust construction, no risk of demagnetization due to overheating, and the ability to freewheel without any electromagnetic losses. Customers have reported that these benefits allow increased range and reduced drivetrain system costs compared to alternatives,” the company said.
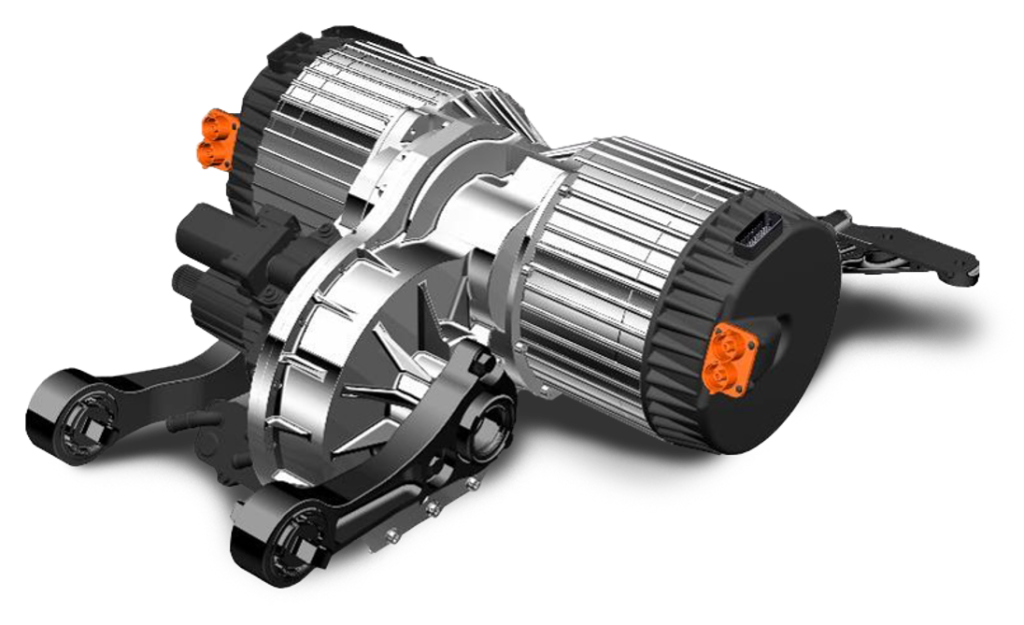
“SSRD takes this technology to the next level, delivering performance benefits that meet industry targets for 2035 today.”
Focusing on high volume applications, SSRD is said to be able to deliver 50% more power for 35% less weight than a leading permanent magnet passenger car motor, while the flexibility of the technology sees on-going developments that are pushing the performance envelope even further to deliver power densities of up to 29kW per liter – more than ten times the original permanent magnet passenger car motor it was designed to replace.
HDSRM has been specifically developed for use in commercial vehicle applications, which require very high levels of continuous performance and a long service life. AEM currently offers HDSRM in three configurations, delivering motors to customers on three continents.
In its standard form, HDSRM300 delivers peak torque of 380Nm and power of up to 214kW, while HDSRM300T increases torque to 520Nm with peak power of 166kW. Both motors weigh 75kg and are liquid-cooled. The smaller, air-cooled HDSRM150C weighs just 25kg and delivers peak torque of 100Nm with peak power of 50kW.
Designed as a modular solution, AEM offers the potential to scale to higher power and torque levels, or several HDSRM can be combined to deliver even greater levels of flexible power and torque and an even broader peak efficiency zone. HDSRM can also be paired with internal-combustion engines acting as both traction motor and generator for hybrid vehicle solutions. AEM also has world class transmission design capabilities developing a gearbox that can support drive from up to three HDSRM motors, achieving a peak torque output of 4200Nm. AEM can also provide bespoke gearboxes with ratios to suit the vehicle’s application.
SSRD has been developed for the passenger car market and its patented design allows systems to deliver anywhere from 125kW as a single motor up to 600kW as a lightweight e-axle. SSRD is extremely cost effective to produce with an inherently lower bill of materials cost than a permanent magnet motor. Add to this a potential 10% efficiency improvement over today’s standard drive cycles, as well as 100% recyclability.
Working closely with world class organizations in the UK, US and Europe to bring next-generation technologies into production, AEM has global ambitions. Manufacturing facilities are in place that can scale to 12,000 motors and beyond to meet near-term demand, whilst work is underway to roll out global expansion plans to meet longer term customer requirements.