Countries around the world have ambitious goals to manufacture the components for electric vehicles, including lithium-ion batteries, to meet the need for the next generation of clean mobility solutions. Industry collaboration will make lithium-ion battery recycling safer, more efficient and sustainable.
There are major opportunities for organizations that can demonstrate expertise and which have the resources to innovate, because they will be solving the issue of what to do with the thousands of lithium-ion batteries that will soon be reaching end of life.
It is predicted that by 2040, 339,000* metric tons of electric vehicle batteries will reach end of life [*source: the University of Warwick’s, Automotive Lithium-ion Battery Recycling in the UK report] which have an average lifespan of around 11 years and contain high value metals such as lithium, nickel, cobalt and copper.
The EU Battery Directive (adopted by the UK) has the primary objective of minimizing the negative impact of batteries and accumulators and waste batteries on the environment. It also states that for all lithium-ion batteries, a minimum of 50% of their weight must be recycled at end of life. This means that there is a great opportunity for manufacturers, recyclers and specialist battery processing companies to work together to ensure that EV batteries can be easy, safely and efficiently recycled for the benefit of all.
Manufacturers such as Nissan and Volkswagen are already investing heavily in end-of-life battery re-use and recycling. This clearly demonstrates that manufacturers are getting involved in ensuring that the batteries utilized within vehicles can be efficiently recycled to reduce complexity at end-of-life stage.
There are greater environmental and workplace risks associated with the dismantling of EVs than traditional petrol or diesel motors. The high voltage of the batteries and the fact that they can easily ignite during the dismantling process, leading to the release of highly toxic chemicals such as hydrogen fluoride, adds to the need for robust safety measures.
An industry-wide commitment to the use of safer, more sustainable materials and standardization in the way batteries are produced and controlled would make a huge difference to the safety and efficiency of the whole process.
This starts with the battery pack, which needs design to be prioritized to ensure they can be easily dismantled at end of life. There has also been a call for an extension of the current International Dismantling Information System (IDIS) to cover batteries. This would provide full visibility over materials and component construction of batteries to ensure end of life recycling can be standardized, therefore the whole process would be much easier and safer using approved practices throughout the industry.
There also a need for open communication protocols for second life battery use, to make the repurposing of batteries easier. A great deal of investment and research & development is going into second life batteries and whether end of life batteries can be re-used in other applications, for example, for energy storage by National Grid or for powering residential-scale solar PVs. The size and scope of this market is still largely unknown and even if it becomes as big a sector as is anticipated, a large amount of EV batteries will still need to be recycled.
Many recyclers are currently sending batteries to Europe for end of life processing, but this is expensive and is not a sustainable way forward. As the number of used EV batteries grows, there needs to be a network of specialist companies which are able to carry out safe and effective lithium-ion recycling in the UK.
EV batteries are renowned for being heavy and moving them brings its own logistical challenges. Authorized Treatment Facilities (ATFs) will have to establish new processes and systems which cater for the additional precautions and increased handling capabilities needed to extract batteries from vehicles. Appropriate training methods are needed to ensure recycling staff are aware of the hazardous nature of components and to ensure health and safety requirements are paramount.
To further reinforce the need for sustainability, there is talk of a Battery Passport being introduced, where every element of the battery is recorded, therefore making it more traceable. Although this may be some way off, it would certainly go in the right direction to ensure that more sustainable batteries are being produced in the future.
What is certain now is that in 10-15 years’ time, there will be a lot of EV batteries hitting the recycling industry – and they need to be handled safely and sustainably.
High-value metal recovery
There are two main methods of lithium-ion battery recycling to recover metals and valuable components. The first is Pyrometallurgy – using high temperatures to melt the battery under controlled conditions then extract the metals from the residue.
The second method is Hydrometallurgy – using a chemical treatment to dissolve metals held within the EV battery. Before chemical treatment can take place, the battery needs to be shredded to open it up and separate its components. Obviously, this needs to be done in carefully controlled conditions as it features potentially hazardous and flammable materials. Currently, these processes are not being carried out in the UK, apart from at our dedicated lithium-ion battery recycling facility in Sheffield. Here we accept secondary lithium-ion batteries from EV and hybrid vehicles for recycling, with a capacity of 1,000 tonnes of cells per year.
From each battery, valuable materials including cathode powder, copper, and aluminum are recovered. These materials remain suitable for onward processing and will create compounds available for use in the manufacture of new batteries.
Looking to the future, regulations should be developed further to aim for a larger proportion of the battery being recycled. The proposed recast of the EU Battery Directive is a step in the right direction and we hope that the UK will follow suit with similar ambition. Hopefully with the right level of investment, backed by legislation and a commitment from the whole industry will mean all EV batteries can be recycled in the UK in the very best, most sustainable way.
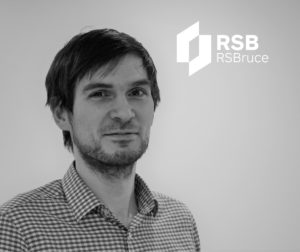