The 1960s was a decade with no shortage of technological, political, social and cultural change. But amid all the upheaval, away from the headlines, General Motors (GM) was quietly going about its business with the testing of the Electrovan – the world’s first hydrogen-powered fuel cell vehicle, and the first use of fuel cell technology derived from US President John F Kennedy’s challenge to NASA to safely land a man on the moon by the end of the decade.
Electrovan was the brainchild of Dr Craig Marks, who headed up many of GM’s advanced engineering projects. It was developed by a 200-person team over a two-year period and tested for 10 months before a driveable tech demonstrator was shown off to the media in the autumn of 1966. Due to its prohibitive cost (the platinum used in the fuel cell was reportedly enough to purchase an entire fleet of vans) and lack of supporting hydrogen infrastructure in place at that time, Electrovan was regarded by GM as strictly a test vehicle to explore hydrogen as an energy source for vehicle propulsion.
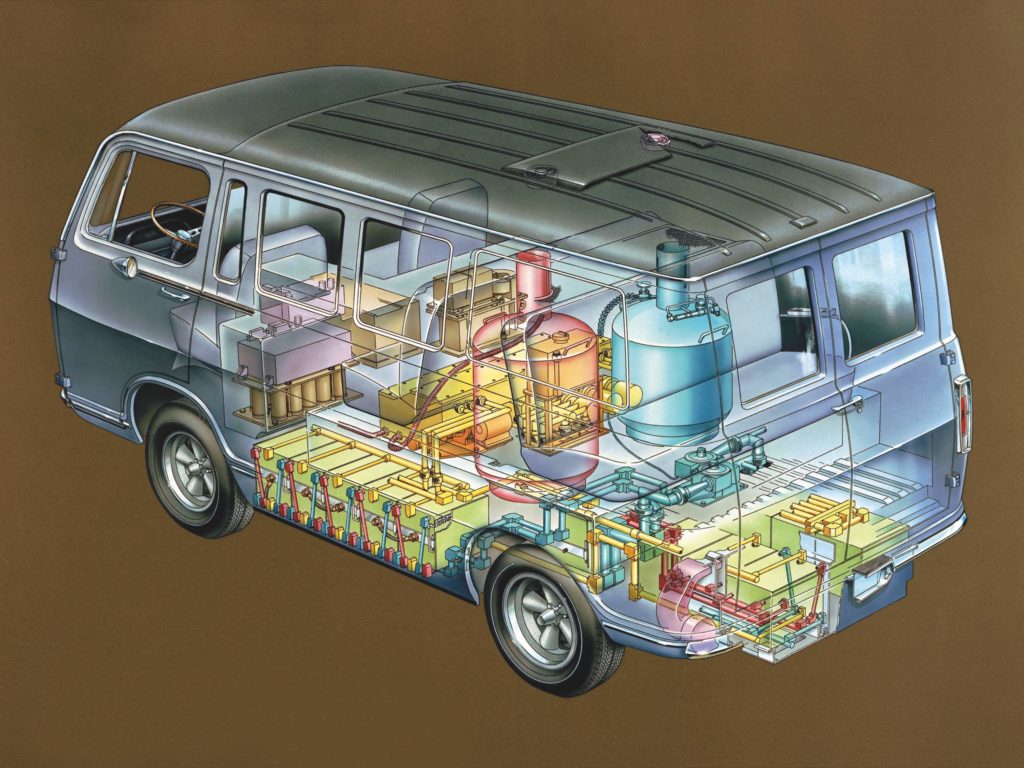
GM tested the world’s first hydrogen-
powered vehicle, but Floyd Wyczalek,
project manager for fuel cell development
on the Electrovan, has clear memories
of working on the innovative venture. Credit: GM Archive
At the end of the project, Electrovan was stored in a warehouse in Pontiac, Michigan, for 31 years before being rediscovered in 2001 and rehoused at the GM Heritage Center (GMHC) in Sterling Heights for public displays. The vehicle has remained there ever since, and when Electrovan celebrated its 50th anniversary, GM marked the occasion by inviting Floyd Wyczalek, project manager of Electrovan’s fuel cell development, to GMHC to recount the test period and, remarkably, to sit inside the vehicle for the very first time. Speaking with E&H Vehicle, Wyczalek, now 91, rolled back the years to discuss what it was like working on the groundbreaking project.
Can you remember how the Electrovan project was first set in motion?
GM adopted a corporate policy of ZEV [zero-emissions vehicles] in the early 1960s. In early 1964, the GM engineering staff division at the GM Technical Center [located in Warren, Michigan] responded by proposing a two-phase solution to support senior management’s ZEV policy.
What did phase one entail?
Phase one was an Ag-Zn [silver-zinc] BEV platform to develop an oil-cooled 75kW three-phase induction motor compact enough to mount in a production vehicle, measuring 20cm [7.9in] in diameter by 25cm [9.8in] long, 13,000rpm, with a mass of 60kg [132 lb]. Dr Paul Agarwal, head of GM Research’s electrical engineering department, coordinated development of the traction motor and IV [infinitely variable] solid-state motor control system. GM Delco Products built the units for our project. Neither component existed at the time. This was called Electrovair and was based on a converted rear engine production 1964 Corvair air-cooled IC piston engine platform.
What can you tell us about phase two?
Phase two was an H2 [hydrogen] fuel cell-powered EV called Electrovan, which was based on a GMC Handivan platform. The Electrovair traction motor and IV motor controls were to be transferred directly into the Electrovan. Consequently, development effort could be focused exclusively on an H2 fuel cell development compact enough to mount in the Electrovan. The fuel cells were a spin-off from NASA’s Apollo lunar program. Fuel cells provided pure drinking water for the three-person lunar mission crew and electric power for the command module and two-person lunar lander. Water exhaust and electric power were also an ideal fit for GM’s ZEV policy.
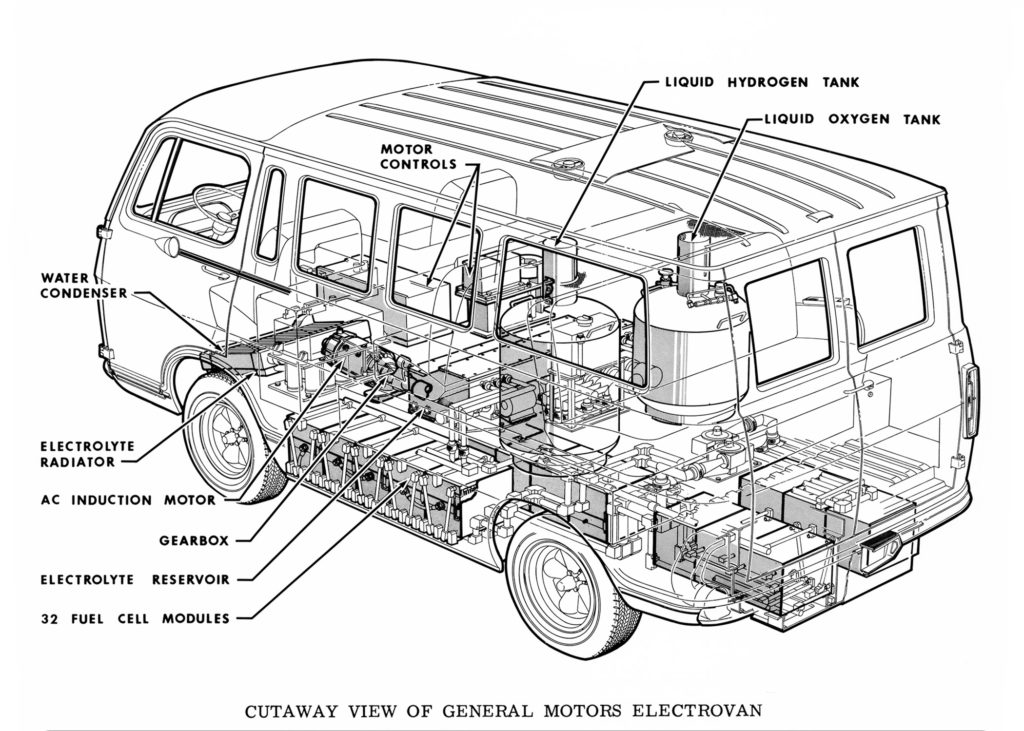
Was a different approach to testing required, compared with those that were designed for fossil fuel-powered vehicles?
Yes, our first challenge was to build a fuel cell powertrain simulator development test facility, which did not exist at that time. In addition, we needed to appoint and train a team of fuel cell powertrain simulator test engineers and technicians. Except for principle engineering staff leadership, most of the engineering team was not familiar with fuel cells. In a hands-on program with fuel cell engineers and technicians from Union Carbide, this joint team then began the process of designing and installing appropriate fuel cell test equipment, starting with an empty test cell.
Which suppliers did you work with on the project?
Hydrogen and oxygen were available from Linde Group and Air Products, two independent companies. Linde installed a 6m-diameter [19.7ft] cryogenic liquid H2 sphere at the GM Technical Center campus and Air Products installed a cryogenic liquid O2 tank at the end of the engineering staff piston engine dynamometer wing. Furthermore, our fuel cell test facility was located at the very end of the dynamometer wing for safety considerations.
What were some of the project’s biggest engineering challenges and how did you overcome them?
We had 32 series-connected fuel cells. Each fuel cell had four submodules consisting of four single cells in parallel plus 17 series submodules per 1kW fuel cell – 68 cells and 17V DC per module – for a total of 2,176 cells. The 32 series-connected fuel cell modules provided 540V DC – two phase +270V and -270V. Consequently, our second challenge was to scale up from a 31-cell Apollo fuel cell module to 2,176 cells – a world-first effort that had never been accomplished previously. Furthermore, H2 gas polypropylene plumbing to the last fuel cell module was more than several meters away from the gas input. Consequently, hydrodynamic fluid transport prevented uniform distribution of H2 to each of the 2,176 cells simultaneously. The result was single-cell polarity reversals by adjacent cells that had activated first. The resident Union Carbide engineers and technicians solved this cell polarity reversal issue by rewiring each 1kW module with 68 individual cell conductors leading to a multiconnector mounted on top of each 1kW module. There was a total of 2,176 wiring connections for the 32 modules, which was another world first.
What were some of the most important tests that you performed on the vehicle?
The fuel cell simulator ran 24/7 for 30 days in a continuous durability test. It found that the KOH [potassium hydroxide] electrolyte was leaching and reacting with the fuel cell neoprene seals hydrocarbon plasticizer. The chemical reaction formed soap deposits within the polypropylene tubing serpentine circulation loops. Soap also plugged KOH passages within the GM Harrison radiator heat exchanger. Furthermore, there were some unseen soap deposits within individual fuel cell KOH passages.
Did you have a sense that you were working on something groundbreaking?
A key function of GM senior management level is to provide policy direction and set the core mission and direction for the company. In turn, the prime responsibility of staff divisions at the GM Technical Center is to recommend solutions in support of GM policy and its core mission. Consequently, engineering staff routinely, as a matter of job description, regularly recommended solutions in support of policy goals. We simply regarded zero-emissions BEV and H2 fuel cell vehicles as routine projects. Doubt never really occurred to us. As examples, prior to and following the Electrovair and Electrovan projects, engineering staff evaluated many other forms of new technology to determine their readiness for commercial production. Project prototypes that demonstrated readiness were transferred directly to a manufacturing division for serial production consideration. For Electrovan, we concluded that potassium hydroxide hydrogen fuel cells demonstrated that a Bacon-type KOH fuel cell was not a viable option in an automotive application.
Acceleration and top-speed tests were conducted on a chassis dynamometer, while fuel cell durability was performed over several months in a test cell. What are your memories of that time?
Driving and durability tests were conducted at the chassis dynamometer wing to ensure driveability, determine a maximum speed of 70mph [113km/h], and 0-60mph [0-97km/h] acceleration of 30 seconds. Final practice driveability evaluations were then carried out on a north-south half-mile straight built along the eastern boundary of the GM Technical Center campus. Practice proof-of-principle demonstration loops were driven past the styling division dome before the international press ZEV H2 fuel cell demo run on October 28, 1966.
Were you satisfied with the project?
Although the press demonstration proved successful, Electrovan was deactivated, reactants purged, and the van moved to the styling division dome interior display area for inspection and photograph by press. We concluded that Electrovan was not suitable for the passenger automotive application and confined it to long-term storage.