Words Richard Gooding
The ‘skateboard’ chassis isn’t necessarily right for every EV. E&HVTI investigates how WAE’s new modular concept has been designed to accelerate the development of high performance sports cars
A modular skateboard platform is right for many EV types, but a bespoke architecture is often needed for more specialist vehicles. WAE’s new EVR electric chassis has been created for start-up and OEM hypercar manufacturers to build high performance sports cars. Alongside EVX, the company’s more traditional modular EV skateboard platform [see Platform Games], EVR has been in gestation for some time. “We’ve had aspirations to make a two-seater sports car around our own battery technology for several years,” states Chris McCaw, WAE chief engineer, vehicle integration. “We spent around 18 months on it prior to the launch in autumn 2022.”
EVR, like EVX, is a turnkey solution. Built around a 2,850mm wheelbase, the rolling chassis is continuously updated with the latest WAE motor and battery technologies. EVR currently supports a motorsport-derived (WAE supplies batteries for both the Formula E and Extreme E racing series) 85kWh lithium-ion battery pack, with peak power of 1,650kW (2,212hp) developed via two, three or four electric motors. Performance is truly electrifying with a sub-2.0 second 0-62mph sprint time, and like EVX, a ‘top hat’ ‘ body solution – targa, coupé or roadster – can either be supplied by the client or designed by WAE styling partner Italdesign Group. Five levels of build can be undertaken starting with the electrified powertrain, through to a complete vehicle make-up.
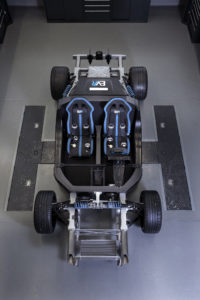
Photo Tom PIlston.
Tailor made
It’s the modularity which is the real key to EVR, allowing for product individualization. “Because the market is so broad, customers don’t like the idea of a reskinned product,” says McCaw. “With a platform that multiple customers can grow from, each customer wants to feel the product is unique to them, while relying on the completed engineering.”
Built from around 15 sections, the core tub forms the heart of EVR, the individual elements manufactured separately and bonded together. This gives opportunities to make small changes to tooling rather than necessitating a more major investment. EVR’s composite monocoque sits forward of an imaginary B-pillar location, and metallic beams pass from the back of the seats to the rear suspension pickup points. The battery module sits in the space in-between. Cradled in a specially designed carbon composite enclosure, the module allows elements of the structure to be removed from the chassis itself.
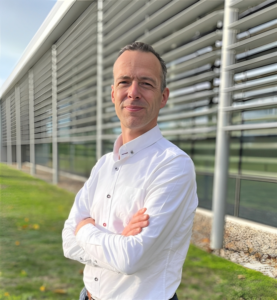
“Companies we’ve worked with previously have had a defined chassis and wanted to put our battery into it. However, the battery can provide a significant structural contribution,” explains McCaw. “Panels on all four sides act as structural stiffeners, allowing us to downsize the rear metallic beams.” Potential rival hypercars use composites to extend front and rear structures, but EVR’s metallic elements allow for increased variation.” “Metallic front and rear extensions allows us to vary the track, wheelbase and powertrain mountings much more easily, depending on configuration,” McCaw says.
All-wheel drive capability
A sophisticated torque vectoring system sends motor power to the wheels. Rear-wheel drive versions with a twin rear axle motor set-up have left-right torque vectoring – in three-motor platforms, the third motor is added to the front axle with a limited slip differential for all-wheel drive capability. The most extreme four-motor platform uses one inboard-mounted motor per wheel, with more adverse road condition capability.
A single-speed epicyclic gearbox is expected to be the default choice, but a dual-speed option is being evaluated for practicality and sustainability. “This allows more opportunities for hitting the very high V-maxes and low-time accelerations, without using larger motors,” says McCaw. “We foresee prices of rare earth metals and magnetics increasing, so if we can deliver the same acceleration and overall performance using less magnetic content, that’s clearly going to be advantageous.”
Newer battery technology may be on the horizon, too, but lithium-ion cylindrical cells give WAE an immediate solution. “There’s some very interesting work being done with new cell chemistry or solid state cells, but they’re not at a point that can be pushed out to the market and delivered in 18 to 24 months, which is what some customers are asking for,” McCaw says. Single charge range is up to 279 miles, the 850V architecture delivering a refill time of under 20 minutes, with up to 550kW of charging power.
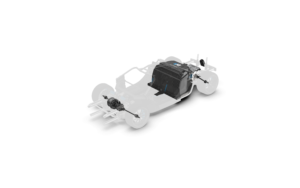
However, efficiency is more important than range, states McCaw. “While we’re not necessarily hitting a WLTP cycle, we are seeing customers desire consistency of performance around multiple laps, rather than just one hot lap. Increasing the powertrain system efficiency not only gives us that range but allows us to decrease battery weight to target a specific distance.” With the need to deliver very short spikes of high power, McCaw explains that the battery management system (BMS) is crucial to help manage the life of the cells. “We have been developing BMS software to look at predictive models of cell aging, including cloud analysis and digital twins of cells within the pack to ensure battery life is extended by another 30 or 50% beyond what would normally be possible.” Integrated in that is how much of the absolute capacity is usable. WAE’s work has enabled it to potentially drop the lower limit down to around 2%, pushing the upper limit up to 98% – around an additional 5% capacity without more weight or batteries.
Crucial competency
Lightweighting is a WAE competency and is crucial to offset the battery weight. Weight for the two-wheel drive, track-focused product is aimed at between 1,700-1,750kg. “Here you get the agility and acceleration without having to put in more batteries, energy, motors and power,” reports McCaw. It’s a delicate trade-off, with even braking system components potentially shaving 200-300kgs out of the car. Saving weight is one challenge WAE is well-versed in, but weight distribution has proved more challenging. “Compared to a skateboard chassis, EVR has a more conventional supercar architecture.” says McCaw. “With between 25-35% of the vehicle weight very close to the rear axle, we’ve had to look at how we redistribute other systems to offset that to bring weight distribution forward.”