Words Frank Millard
The relentless move towards the decarbonisation of the automotive industry involves the coordination of various elements, the most important being issues pertaining to battery technology. Energy density, safety, cost, gigafactory development and mineral supply are crucial to reaching 2050’s net zero target, and nowhere is that better understood than at UTAC Millbrook proving ground.
In February 2021, Millbrook Proving ground in the East of England merged with the French automotive testing group UTAC CERAM to combine their experience and expertise in vehicle testing, homologation, and emerging technologies for autonomous, connected, and electric vehicles. As part of the merger, a battery test facility, powered by microgrid, was built from scratch, and purposely designed for the application. “It was a great way to start,” says battery testing manager Peter Miller, “It wasn’t retrofitting something, we actually had a clean sheet of paper.”
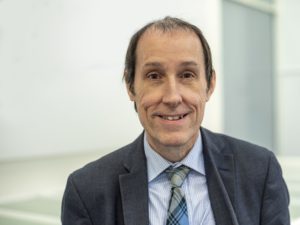
In addition to providing full vehicle test facilities including electric vehicle (EV) and fuel cell vehicle (FCV) crash testing, and a range of electric machine and inverter tests, Millbrook offers battery pack life and performance testing, cell and module life and performance testing, battery shock testing, battery safety and abuse, including battery drop and nail penetration testing.
The company’s target customers are automotive manufacturers and suppliers operating in Europe with requirements for the proving ground’s battery lab and fire testing laboratory, “We also have conventional test facilities,” says CEO Laurent Benoit, “Such as the crash-test sled, which also allows us to test batteries or EVs.”
However, while car manufacturers and suppliers are working very hard to meet the future environment regulations requirements, it is an ongoing challenge, consisting in adapting in near real time to market fluctuations, especially in Europe and the USA, says the CEO. “The job of UTAC is to adapt to the demands of its customers, to always go faster,” he says. “The expertise of our employees, our work organisation and the efficiency of our resources allow us to provide an efficient, fast and reliable response to our customers.”
Bigger is better
The proving ground’s facilities and test equipment have been designed by its own engineers or manufactured to its specifications, then carefully calibrated, and used by a very experienced team. This gives the facility the flexibility to do almost any test within a very safe environment, which ensures great reproducibility – a key requirement if the results are being used to gradually refine a design, says Miller.
One might reasonably ask, why can’t UTAC Millbrook’s customers carry out the testing themselves? “Some of our customers believe they are better using their own capital to invest in new designs and production facilities,” says Miller. “Also, by supporting multiple customers we can justify investments that would not make sense for any one company. High utilisations also enable us to use automation, optimise work flows and focus and accuracy and reproducibility to a degree that would be hard for a customer who only did their own testing to justify. Our larger customers may have some facilities internally, in which case UTAC provides them with a flexible ‘overflow’ capability, while also offering capabilities they don’t have.”
The industry has reached a point where batteries for EVs, plug-in hybrid electric vehicles [PHEVs] and hybrids are good enough for mass market use, and that is clearly visible from the sales figures – the Society of Motor Manufacturers & Traders [SMMT] data for year to August 2022 shows about 1/3 of vehicles sold in the UK were battery electric vehicles [BEV], PHEV or HEV, and around another 1/5 were mild hybrid cars [MHEV]. Conventional petrol and diesel vehicles accounted for only 50% of sales.
“There are still many ways batteries can be improved, but the focus in the industry is now more on scaling up with gigafactories and ensuring there is a robust recycling process is in place,” says Miller. “We cannot just throw away the materials batteries and whole vehicles contain when they reach the end of their life.”
All staff at UTAC Millbrook are required to have passed at least an introductory training course on alternatively fuelled vehicles (AFCs), such as EVs and FCVs. “This includes critical safety information, knowledge of relevant procedures etc,” says Miller. “A significant portion of the company’s capital investment is related to this.”

From thought to road
Millbrook can test from a very early stage, potentially starting with factory modules, packs, and vehicle prototypes through to volume production from different places. “The people who originally developed the chemistry may not be the people who put it into manufacture,” says Miller, “And then the people who build the battery pack may be from a different organization to the people who build the vehicle.”
An increase in simulation work is reducing the amount of physical testing that takes place at the end of the development process, but both are increasing. Miller says that, typically, there is a new type of lithium-ion battery or a subtle change every six months: “Rather than a vehicle being built for 10 years and not evolving very much in that period, now, there’s a new model or an upgrade every year or two, with a new battery in it,” he says.
The vehicle itself might only have an occasional minor facelift, but new types of lithium-ion batteries and subtle changes mean a lot of testing. Miller points out that the physical testing of batteries is increasing, but so too is simulation due to battery size and the development of automated vehicles [AVs]. There are many potential road risks that are difficult to test for without using some element of simulation. Now more than ever, it’s an essential part of the development process. Generally, there is an 18 month to two-year development period for a new battery or batteries, so simulation testing is required to prove one’s virtual prototype. Even if there is a turning point and manufacture is begun without the construction of a physical version. Once in production, then field data can be gathered.
Battery testing
Assessing how and in what ways a battery or vehicle will age is an important part of EV testing. “First of all, you can’t accelerate the testing by making it very hot, which is traditional way of doing it,” Miller explains. “Internal combustion engines [ICE] have been made for over 100 years now, and we know how to accelerate ageing, which typically that involves running them hotter.”
Unlike an ICE vehicle, an EV is either being driven or charged. “You can’t say an EV is only being driven an hour a day and ignore other times. When it’s being not driven, it’s plugged in and being charged.” The tests need to mirror what would happen in the real world, which in this case is near continuous use.
Temperature is the primary factor that affects the aging of an EV battery, says Miller. “Normally, the maximum rate of charging and discharging is limited by other factors, but there tends to be a fundamental limit as to how fast you can safely charge and discharge the cells based on the chemistry.”
Whereas, the testing of a conventional vehicle is quite straightforward, if a battery is heated much above ambient temperature there can be chemical side reactions. Many vehicles run quite close to the limits, says Miller. “People are trying to get charging times down and 350-kilowatt charging is now becoming common for vehicles, which in many cases, would be a higher power than one would actually use when driving.”
Making allowances for a varying of the temperature is also a consideration given that the changing of the seasons can affect battery life: “Using it when it’s cold, is not particularly good for a battery,” says Miller.
The tests for performance and life, have not changed very much though. “The basics of how we do the testing, haven’t changed in my career,” says Miller. “For 40 odd years, you put energy in, and you take energy out, you vary the temperature. The automation behind that, and the accuracy and repeatability have improved. Because clearly, one thing that’s critically important is that you get as reproducible results as you can from a test, because as you’re working through the design process. But one thing you want is test data that you can feed into your simulation, because clearly, part of this must be done through simulation.”
There is also a string of tests required to validate a battery as safe enough to be used and that includes the pack, says Miller. “That starts with the cell then goes on to monitoring, testing, and then up to pack one and ultimately the vehicle test.” Safety testing includes gas detection and fire risk.

Best of both worlds
At UTAC Millbrook taking both a real-world usage and potential-failure mechanism simulation approach is the most comprehensive way of getting their customers the results they require. “We do a mixture of both,” says Miller. “Some of the tests are focused on moisture. So, you might have a test that was purposely designed to go through the dew point to make sure that the sealing of the battery pack was sound. You could heat the pack to pass through the dew point to try and maximize the amount of humidity generated if that’s your focus. So, we can get condensation surface, fog, and most dry changes, for which there is a drain in the floor.”
Full immersion testing is also available, where the battery can sit in a test chamber for two years replicating 10 to 15 years of real-world driving. However, EV testing is more about integration of all the systems rather than looking specifically at the performance of the battery.
“When we’re testing here, we’re still relying on simulation to predict the environmental boundary, but no simulation is perfect,” says Miller. “We still need to do some real-world testing, which is why we’ve got vehicle chambers and the tracks and then ultimately you need to drive a vehicle and put the miles on it, and it’s likely we’ll find some issues that were missed all the way through the design process.”