Words John Challen
The Lunaz brand has quickly become synonymous with keeping classic cars on the road with an electric powertrain for the future, much to the delight of the owners. As impressive as that operation is, the opportunity to open the ‘upcycling’ approach stretches way beyond the likes of Rolls-Royces Phantoms, Jaguar XK120s and Range Rovers. For a viable business proposition, volume is required.
Step forward the company’s latest venture, Lunaz Applied Technologies, which opened its doors in Silverstone, UK in February. Primarily concerned with the conversation of refuse trucks at the end of their first lifecycle, the new production facility – which is just down the road from Lunaz Design – will see more than 1,000 vehicles through it every year. And that’s just the beginning. David Lorenz, founder and CEO, Lunaz, has high hopes for not just the facility, but also the wider business model to prevent what he calls ‘carbon postboxing’ – effectively moving products to another part of the world at the end of their first life on the road. “Operators are being asked a lot of regarding meeting emissions targets and we want to enter the market and support them in the right way,” he states. “Upcycling is vital to the future of transportation – we need to put an end to the process of buying and replacing vehicles. If you reuse and recycle, you can improve things one vehicle at a time.”

Lorenz says that beyond the financial conversation, there’s a wider issue at play. “Our vehicles are probably less expensive than buying a new EV – that’s the actual key fundamental: it’s greener and a less expensive production process,” he maintains. “That means we can save local councils and taxpayers millions, which is essential, but also, the workforce get a higher quality product than many standard vehicles available on the market.
“We’ve been in discussions with local authorities for some time, but we needed to complete the factory and demonstrate our battery technology that is going to be used on the vehicles,” adds Lorenz, who details the potential demand for the Lunaz refuse truck. “We’re in touch with around 50 local authorities as well as most of the top 10 private waste management companies in the UK, who are compelled for several reasons. Firstly, they see us as a good technical partner, and they feel we are doing things in the right way. They also see the functional advantages and technological upgrades that can be tailored to the specific requirements of their fleets. There’s also a simple performance function as well, which is as much about our engineering as the upcycling process.”
While Lunaz Design is a project-focused business, Lunaz Applied Technologies (LAT) is designed to be a volume production operation, which means there are fewer concerns about having to seek specific components for vehicles, and more worries about productivity and efficiency. The timescale for a vehicle entering the facility in its original state to going out of the door as a converted Lunaz truck is 14 days. In that time, a lot of work is done beyond taking out the engine and popping in some batteries. “The main goal is to improve the overall quality of the base vehicle,” says Lorenz. “Fundamentally, each refuse truck is stripped down, before all the components are assessed, the chassis is shot-blasted and then we stress test it for fractures, etc. It is then painted and rebuilt with all the original moving components – such as air lines, airbags, suspension, brakes as new and then we start the rebuilding process because everything is done on the production line.”
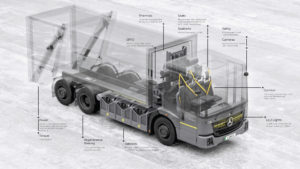
Proof is in the product
Drivability is in important factor, it appears, even for those who might ‘just’ be driving or being a passenger in a truck collecting trash. “There are mainstream refuse collection vehicles on the market that don’t have a transmission, therefore you’ve got a difficult compromise between top speed or hill climbing ability,” says Lornez. As a response to that, he explains that the Lunaz product has been to Millbook and put through their paces. “Our vehicles can climb a 1:4 slope, stop halfway up and then go again. But they can also do 56mph, which is electronically limited. Potential customers are coming to us, because they have been – to a point – brought in by the sustainability aspects in the embedded carbon aspects of EVs and the fact that there’s cost saving. Then they realise that the vehicles are just very good – from both a technology and performance point of view.”
Physical and climatic testing also takes place at Millbrook, while Lunaz confirms that a trip to Northern Sweden is in the offing for the most extreme evaluations of the powertrain technology and other major components. Closer to home, the road network around the facility – complete with conveniently placed bins – provides the ideal test route to check battery degradation.
What was important was to start with a blank sheet of paper when it came to not just the vehicle, but also understand the customers and drivers – predominantly those operators on council or local authority fleets. For this understanding, Lunaz staff joined interested operators on their rounds, to get a better idea about their requirements when it came to the electric vehicle they would be stepping into, having seen an end to the diesel engine-powered models.
“Obviously, some fleet operators – especially some major operators in the UK – have a huge amount of data about their vehicles and the duty cycles,” explains Lorenz. “We like to gather all that data and, if there is no data, we investigate its entire fleet and then we can work out their requirements from there. Many of the vehicles are running the same route day in day out and, at that point, you can specify the vehicle for its absolute requirements.”
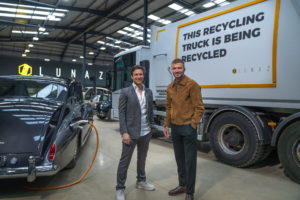
The big build
Lorenz says the company is ready to deal with all sorts of requests for conversions of up cycling projects. “Some operators will have the vehicles already and, using the platforms that we’ve created, we will look to transition them to EV down our production line. However, other customers might not have the vehicles because they may want to move away from their current product and take on what we are producing.” For those customers, because the main Lunaz finished article is based on the Mercedes-Benz Econic platform, it would involve the company acquiring vehicles from the marketplace. “I really like this approach because we’re stopping these vehicles going on cargo ships going off to other countries and end up in the cycle of ‘carbon postboxing’, which needs to stop,” says Lorenz. “Fundamentally, as we looked at the global emissions crisis, not the local emissions crisis, we found ways to break that cycle and we are confident we can make a difference.
“We are agnostic to vehicle brands,” he stresses. “We’ve done the engineering programme around the Econic platform, but also we’re about to embark on another project looking at a different vehicle category. We are really focused on vehicles with a duty cycle we can really understand. There are so many vehicles that do the same route day in, day out, where this philosophy of tailoring a vehicle for its requirements gives us a USP – and the more specialist the equipment, the more value you’ll add into that vehicle.”
At present there are two production lines and four different assembly spaces within the LAT. The longer-term plan is for a further two lines, depending on levels of demand for the company’s services. Beyond Silverstone, there are further – more ambitious – plans. “What gets us really excited is how the business can scale because the remanufacturing is recorded, measured and audited,” explains Lorenz. “That means we can copy and paste factories like this around the world. And that’s how this business will grow from 1,100 units here to many more all over the world. However, this will always be its home – it’s the data engineering hub, the master facility, the blueprint!”