Advanced Electric Machines (AEM), a UK-based manufacturer of sustainable motors, has unveiled the second generation of its heavy-duty electric motor solution. The new HDRM300C builds on the company’s existing technology with improved performance and efficiency for commercial vehicle applications.
The motor utilizes AEM’s innovative compressed coil technology, which achieves over 80% conductor slot fill rate compared to the conventional 60% found in traditional motors. This design, previously validated in the company’s smaller HDRM150 motor, has now been scaled up and refined for heavier applications.
Enhanced thermal management and cooling design enables the motor to deliver better continuous performance, while a higher top speed provides greater flexibility for different uses. The cooling system, which functions similarly to a car’s radiator, allows the motor to work harder for longer periods without overheating – a crucial feature for commercial vehicles that need consistent performance throughout the day.
“The HDRM300C represents more than just an incremental improvement in motor technology,” says James Widmer, CEO of AEM. “By combining our patented coil compression technology with enhanced thermal management and improved speed capabilities, we’re delivering a motor that sets new benchmarks for efficiency and performance. For the transportation industry, this means more capable electric vehicles that are more cost effective to operate and maintain.”
Practical improvements include new plug-in connectors that replace traditional gland fittings, simplifying installation and maintenance while improving reliability. Internal components, including upgraded bearings and busbar connections, have been strengthened to support higher operational speeds.
A key selling point for AEM’s motors is their rare-earth free design, positioning them as a more sustainable alternative to conventional electric motors that typically rely on permanent magnets containing rare earth elements.
Sample units will be available for select partners beginning March 2025, with full production scheduled to commence in the fourth quarter of 2025. The motor is targeted at manufacturers of heavy-duty and commercial EVs.
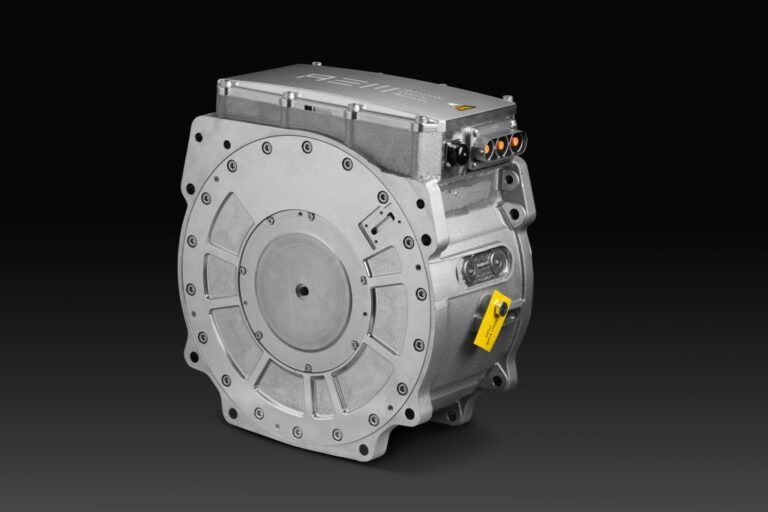
The compressed coil technology achieves over 80% conductor slot fill rate compared to conventional 60%